How to increase electrical safety in the workplace
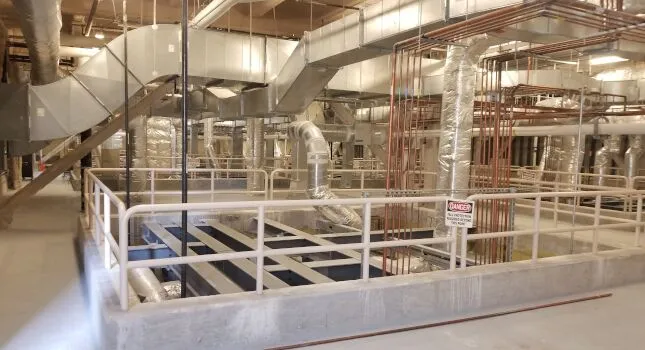
Electrical safety insights
- Proper signage and labeling are crucial for electrical safety in buildings. Compliance with codes and standards ensures the well-being of operators and helps organizations avoid legal and financial liabilities.
- Safety protocols and risk assessments are essential for maintaining safety on construction sites.
Evaluating the safety of existing buildings requires a multifaceted approach that includes both macro and micro analyses of environments, behavior and proposed and existing conditions.
The following safety aspects are particularly important to evaluate electrical safety:
-
Equipment signage and labeling.
-
Safety protocols and risk assessments.
-
Alertness and physical health.
-
Trip hazards.
-
Jobsite electrocution and ground fault circuit interrupters (GFCI).
-
Solar and microgrid electrical safety.
-
Electrical equipment safety.
Electrical safety signage and labeling
Electrical systems are vital for modern infrastructure, powering various equipment and providing energy for daily operations. However, without proper signage and labeling, these systems can pose significant risks. Signage and labeling play a crucial role in providing clear and concise information about the electrical distribution system. They serve as visual cues, helping building operators identify and understand various components, circuits, switches and equipment.
By clearly indicating voltage levels, circuit breakers, disconnects and emergency shut-offs, signage and labeling enable operators to make informed decisions while working on or near electrical systems.
Accurate and visible labeling enables operators to quickly identify specific circuits or equipment, minimizing the risk of accidental contact with live electrical parts. Clear instructions regarding safety procedures, warnings and emergency contact information can also be included on signage, ensuring that operators have access to crucial information during critical situations.
Signage and labeling promote compliance with electrical codes and standards as well as to ensure regulatory requirements are met. Compliance not only ensures the well-being of building operators, but also helps organizations avoid potential legal and financial liabilities.
Reference codes and standards to review include:
-
NFPA 70: National Electrical Code (NEC, 2023 edition): The NEC includes various warning sign (label) requirements for equipment and areas. Article 110 includes the general requirements, such as the requirement to warn for high-leg delta wires, quantify arc-flash hazards, identify disconnects, list available fault current and restrict areas to unqualified persons. Additional signage requirements are included throughout the NEC such as when there are multiple service entrances or an emergency power source.
-
NFPA 70E: Standard for Electrical Safety in the Workplace (2024 edition): NFPA 70E includes the information that should be contained on arc-flash hazard warning labels. NFPA 70E also includes the personal protective equipment (PPE) needed based on the electrical hazard.
-
ANSI Z535, Safety Alerting Standards (2011 edition): ANSI Z535 includes six safety standards to define safety colors, symbols, signs, labels and tags. Specifying engineers should make sure any project specific labeling requirements do not conflict with ANSI standards.
Labeling plays a crucial role in personnel safety by providing information. Safety labels should identify hazards, while informational labels assist in understanding equipment connections and operation instructions. NEC Section 408.4 includes revisions to the text to identify labeling that should be available during the planning and review stages, not just the installation stage. This section lists the requirements for descriptions on switchboards, switchgear and panelboards.
Receptacle faceplates should include panel names, circuit numbers and control types. Color coding, as required by certain standards, can be used to quickly identify systems and their associated components. Maintaining accurate records of arc flash values, fault current calculations, selective coordination study results and panel locations is necessary for safe operating conditions. Documentation should be updated with system changes and breaker settings along with selective coordination study results should be considered living documents.
The physical arrangement of the electrical distribution system, including riser diagrams and floor plans, should be updated with each project to provide accurate information for designers and facility personnel. Adhesive labels, following the standards of UL 969, should be used for labeling purposes. Improving documentation requires simplified equipment nomenclature and precise naming of breakers during an arc flash study. Breaker numbering can facilitate setting, testing and commissioning processes.
Tables containing breaker settings should be easily readable and any differences between the field and software should be communicated. Shading tables and documenting previous settings can help reduce errors. Mechanical dials on breakers require accurate terminology and required settings should be documented and accessible.
In emergency situations, signage and labeling become even more vital. Clear identification of emergency shut-offs, exit routes and evacuation instructions can save precious time and help operators respond swiftly and safely during crises. Regular maintenance and updates of emergency signage and labeling are essential. As electrical systems evolve, equipment is replaced or modified or new regulations are introduced, it is crucial to keep signage and labeling up to date. This helps maintain accuracy, reliability and effectiveness, ensuring that building operators always have access to relevant and reliable information (see Figure 1).
Figure 1: A flow chart to determine signage categories. Courtesy: IMEG Corp.
Electrical safety protocols and risk assessments
The Occupational Safety and Health Administration (OSHA) defines the hierarchy for safety protocols in order of most to least effective:
-
Elimination: remove the hazard.
-
Substitution: reduce the hazard by doing something else.
-
Engineering controls: prevent the hazard with physical solutions.
-
Administrative controls: reduce the hazard through policy or procedure.
-
PPE: physical protection of the worker to reduce injury.
PPE selection is specified by the construction site authority, the facility and OSHA, but beyond those requirements, performing risk assessments for the specific hazards is necessary to maintain safety on construction sites, particularly during daily visits. Construction sites are dynamic environments with various hazards. While PPE does not reduce or eliminate the hazard itself, wearing appropriate PPE can significantly reduce the severity of injuries and accidents.
Construction sites often involve heavy machinery, tools, falling objects and exposure to hazardous substances. PPE, such as hard hats, safety goggles, high-visibility vests, gloves and steel-toed boots, acts as a barrier against these potential dangers. They help prevent head injuries, eye injuries, cuts, burns and other physical harm. Gloves are an important item for jobsite visitors that may come in contact with chemicals, irritants or allergens that may be present on handrails or other surfaces prone to contact.
By conducting risk assessments, construction site managers can identify the specific hazards present each day and determine the appropriate PPE required for daily visits. A risk assessment involves evaluating the tasks to be performed, the equipment and materials involved and the surrounding environment. This assessment should also focus on eliminating or substituting the hazards.
During the risk assessment process, factors such as the nature of the work, the presence of hazardous substances, noise levels and the likelihood of falls or impact should be considered. By analyzing these factors, site managers can determine alternative procedures or policies and which PPE items are necessary to effectively mitigate the identified risks. For example, if there is a risk of falling objects, hard hats and safety goggles should be mandatory, while tasks involving hazardous chemicals may require respiratory masks and chemical-resistant gloves (see Figure 2).
Figure 2: Care is required when opening doors to electrical equipment — interior components must be considered energized and personal protective equipment (PPE) worn until equipment is proven to be de-energized and grounded for safety. Courtesy: IMEG Corp.
The use of PPE and performing risk assessments also demonstrate a commitment to legal compliance and regulatory standards. Construction sites are subject to various safety regulations, such as those set by OSHA. Adhering to these standards not only ensures the well-being of workers, but also helps organizations avoid penalties, legal issues and damage to their reputation.
Additionally, PPE and risk assessments contribute to a culture of safety on construction sites. When workers observe their supervisors and colleagues wearing PPE consistently and engaging in risk assessment practices, it fosters a sense of responsibility and promotes a safe working environment. This culture of safety extends beyond daily site visits and becomes ingrained in the work habits and attitudes of all individuals involved.
It is crucial to provide proper training and education to workers regarding the importance of PPE and risk assessments. This includes instruction on how to select, wear and maintain PPE correctly, as well as training on risk assessment techniques and hazard recognition. Regular reinforcement of these practices through toolbox talks, safety meetings and ongoing supervision ensures that all workers remain vigilant and committed to maintaining their own safety and the safety of others.
Alertness and physical health
As professionals involved in the design and construction process, building designers’ presence on-site is crucial for ensuring that the project progresses smoothly and aligns with the intended vision. Being alert and hydrated is essential to not only maintain personal well-being but also to enhance decision-making, communication and overall effectiveness.
Being alert allows building designers to actively observe and assess the progress and quality of the construction work. By paying close attention to details, they can identify any potential issues, deviations from the design plans or discrepancies that may arise during the construction process. This heightened awareness enables them to make timely adjustments, provide clarifications or propose solutions to problems that could otherwise lead to costly rework or delays.
Alertness is also closely tied to effective communication. When building designers are alert, they are more likely to engage in meaningful conversations with project stakeholders, including contractors, subcontractors and other on-site personnel. Clear and concise communication is vital to address any concerns, convey design intentions and ensure that everyone involved has a shared understanding of the project goals. Alert designers can actively participate in discussions, ask relevant questions and provide valuable input to keep the project on track.
Hydration is equally important for building designers during site visits. Construction sites often expose individuals to physically demanding conditions, such as extreme temperatures, dusty environments and strenuous activities. Proper hydration helps maintain cognitive function, concentration and overall physical well-being. Dehydration can lead to fatigue, dizziness, reduced mental acuity and impaired decision-making abilities, which can compromise the effectiveness of on-site assessments and decision-making. In addition to physical well-being, hydration also plays a role in maintaining a positive professional image.
Clients and project stakeholders expect building designers to exude professionalism and competence. By staying hydrated, designers can avoid physical discomfort, such as dry mouth or excessive sweating, which may distract them or create a negative impression. Being well-hydrated allows designers to remain focused, energetic and engaged throughout their visits, enhancing their credibility and the perception of their expertise.
To ensure alertness and hydration during jobsite visits, building designers should adopt certain practices. They should prioritize getting adequate rest before the site visit to avoid fatigue. Additionally, they should plan their visits during suitable times of the day, considering weather conditions and potential high-stress periods. Carrying a water bottle and taking regular breaks to hydrate is essential. Designers should also dress appropriately for the site conditions, considering both comfort and safety.
Trip hazards
Trip hazards present additional risks in electrical installations and around construction jobsites. They can lead to accidents, injuries and damage to electrical systems. Several common trip hazards exist in these environments, each with its potential consequences.
For example, loose or improperly secured cables or wires for temporary installations pose a prevalent trip hazard. When left unsecured or strewn across walkways, they can cause injuries and potential damage to the electrical system, so projects need to take temporary cabling pathways into consideration.
Temporary installations, such as scaffolding, lighting or power sources, can introduce additional trip hazards if not properly secured or positioned. Ensuring stability and proper maintenance of temporary installations is essential to prevent accidents and injuries. Figure 3 illustrates temporary cabling secured to the ceiling to prevent it from being subject to damage or being a trip hazard in the generator room during construction.
Figure 3: Cabling hung from the ceiling during a paralleling switchgear upgrade project demonstrates how to keep employees safe during temporary projects. Courtesy: IMEG Corp.
Tools, equipment and materials are expected around construction sites, but they can also obstruct walkways and create trip hazards. Hand tools, piping, packing material and other equipment should be stored properly when not in use to prevent accidental tripping. Engineers should pay close attention to what is on the ground when doing site inspections.
Uneven surfaces, such as damaged flooring, cracked pavements or unfinished construction areas, are another common trip hazard. Workers and visitors may easily stumble or lose their balance when encountering such surfaces. Regular inspections should be conducted to identify and address any uneven surfaces promptly.
The 2023 edition of the NEC added a new section to 110.26(A) about grade, floor or working platform. Section 110.26(A)(6) requires that the working space be “as level and flat as possible,” meaning housekeeping pads will now need to match the shape and size of the equipment with minimal protrusion. Figure 4 illustrates the previously acceptable practice of using large housekeeping pads sized for various equipment.
Figure 4: NFPA 70: National Electrical Code (NEC) has changed housekeeping pad requirements, so pads the same depth as the space are no longer allowed. Courtesy: IMEG Corp.
Stairs and steps within a building can also present trip hazards if not designed, constructed or maintained properly. Improper riser height, inadequate lighting, missing or damaged handrails and slippery surfaces can contribute to accidents and falls. Older buildings will have a variety of stair riser heights and requirements for stair landings have evolved over time so “look before you step” is an important rule to follow in any building.
Debris, waste materials and discarded packaging are often found in construction sites and can obstruct walkways, increasing the risk of tripping. Regular cleaning and waste management practices should be implemented to keep the work area clean and free from clutter.
Insufficient or inadequate lighting in work areas can significantly contribute to trip hazards. Dimly lit areas make it difficult for individuals to identify potential obstacles or changes in elevation, increasing the risk of tripping. Adequate lighting should be provided in all work areas to ensure clear visibility and prevent accidents. It is common for existing electrical rooms, especially in older buildings, to have failing fluorescent lighting and excessive shadowing in the room. Designers should attempt to correct for poor lighting levels when project scope allows, which requires early identification when the project budget is in development.
Jobsite electrocution and GFCI protection
According to OSHA, electrocution is one of the leading causes of fatalities in the construction industry, accounting for nearly 9% of all construction-related fatalities in 2019. These statistics highlight the gravity of the issue and emphasize the need for effective preventive measures. One example of required and important protective measures that can greatly reduce the risk of electrocution are GFCIs.
GFCIs are electrical safety devices designed to quickly detect and interrupt electrical ground faults. They monitor the flow of electrical currents and can detect imbalances that occur when a current leaks from its intended path, including when it goes through a person. GFCIs are commonly used in areas where electrical equipment is near water, such as bathrooms, kitchens and outdoor locations. When a ground fault is detected, GFCIs immediately cut off the power supply, reducing the risk of electric shock and potential electrocution.
Arc fault circuit interrupters (AFCIs), on the other hand, are specifically designed to detect electrical arc faults, which are caused by damaged or deteriorated wires and cables. AFCIs continuously monitor electrical circuits for signs of arcing and disconnect the power when a fault is detected, mitigating the risk of fire. While implementing AFCI on the jobsite will not decrease electric shock hazards, the use of AFCI on temporary lighting circuits can reduce the risk of property loss caused by electrical fires.
In the 2023 edition of NEC, 210.12 expands the scope for AFCI to other buildings by replacing the title “dwelling units” to “means of protection” and 2012.12(D) is titled “other occupancies” with an expanded list of applicable areas.
Solar and microgrid concerns for electrical safety
Electrical safety is a critical concern for both in-process and completed solar and microgrid installations. These installations involve the generation, distribution and use of electrical energy, presenting unique challenges and potential hazards that must be addressed to ensure the safety.
During the installation phase, several electrical safety concerns arise. Firstly, working with photovoltaic panels and associated electrical components requires proper training and understanding of electrical hazards. The voltage and current levels involved in solar installations pose risks of electric shock and arc flash incidents if proper safety precautions are not followed. Workers must be equipped with PPE such as insulated gloves, safety glasses and arc flash-rated clothing. Solar panels can present an electrical hazard at any point in the installation process due to their ability to produce voltage potential with even minuscule amounts of ambient lighting.
Additionally, the interconnection of solar panel systems to the existing electrical grid introduces potential dangers. Proper grounding and bonding techniques are essential to allowing overcurrent protective devices to properly function during electrical faults. Bonding of exterior conductive surfaces can reduce the damage from lightning strikes by providing a low impedance path to ground. The installation of appropriate disconnect switches and surge protection devices is also crucial to safeguard against electrical surges and voltage fluctuations. These systems need to be properly selected and labeled in compliance with 2023 NEC 705.10 (see Figure 5).
Figure 5: An example of a solar panel inverter showing signs of age and deterioration from outdoor exposure. Courtesy: IMEG Corp.
Once an electrical installation is completed, ongoing electrical safety concerns persist. Regular maintenance and inspections are necessary to identify any issues that may compromise the system’s safety and performance. This includes checking for loose connections, damaged wiring or potential sources of electrical arcing. Faulty wiring, improper installation or equipment malfunctions can lead to electrical fires.
Adequate fire suppression systems and protocols should be in place and emergency response plans must be established to address potential fire incidents. It is also important to ensure that all personnel who interact with electrical installations, including solar or microgrid systems, receive proper training on electrical safety practices. This includes understanding the risks associated with the equipment, safe maintenance procedures and emergency response protocols. Equipment will age and worsening conditions will require frequent inspection and assessment (see Figure 6).
Figure 6: Solar installation with loose cabling subject to damage. Courtesy: IMEG Corp.
Electrical equipment safety
NEC has continued the tradition of enhancing electrical system protections over previous editions. These enhancements include definitions of “accessibility” and “energized” in Article 100, arc flash labels in 110.16, egress and working space impacts in 110.26, barrier requirements in 215.15, selective coordination requirements in 241.11 and 700.32, fire resistive construction in 450.21 and environmental conditions in 500.7 and 505.8.
It is crucial for facilities to assess the condition of their electrical systems and consider the importance of each component through a risk assessment. If the failure of a system could potentially harm building occupants, then reliability becomes a high priority.
One vulnerability that needs attention is the testing method for generators. In some facilities, the testing methods may not follow NFPA 110: Standard for Emergency and Standby Power Systems to accurately simulate outages and it may be years between actual outages. This presents a situation where the facility does not have experience with the impacts caused by actual outages. It is recommended to perform testing by opening the circuit breaker that feeds the normal side of the automatic transfer switch. This method allows the facility to evaluate the system’s behavior during an outage and identify any delays that need to be addressed.
Another concern is the location and environment of electrical equipment. Unconditioned areas, such as electrical rooms without heating, ventilation and air conditioning (HVAC) or direct venting to the outdoors, can lead to temperature fluctuations, humidity changes and high dirt accumulation, which reduce equipment longevity and increase the risk of failure.
Rooms with generators are particularly vulnerable due to the need for exterior cooling and combustion air. Facilities should implement cleaning and inspection procedures for electrical distribution equipment in these environments. Age is another factor that affects the reliability of electrical systems. Components older than 40 years pose a higher risk of failure. Circuit breakers can internally fail, handles can break off and aging equipment becomes difficult to replace.
It is essential to evaluate the ratings and actual wire sizes of panels and equipment as part of a short circuit current study. This study should also include selective coordination and circuit breaker setting recommendations to minimize the risk of cascading outages. A holistic approach to electrical safety is required and will include both equipment and environmental considerations.
Learning Objectives
- Understand safety related to electrical equipment.
- Identify what electrical safety behaviors can impact people’s health and well-being.
- Know how to create a safe environment around electricity.
The post "How to increase electrical safety in the workplace" appeared first on Consulting-Specifying Engineer