Bringing Facilities Management and Logistics Together with a CMMS
This year marks the sixth-annual celebration of National Logistics Day on June 28βan occasion meant to highlight the essential role logistics teams play in the worldβs economies and communities. Working together with facilities managers, logistics professionals serve as the backbone of international commerce, ensuring the safe storage and efficient movement of goods all across the world. From inventory management and warehousing to last-mile delivery, FM and logistics pros not only support organizational success but also play a vital role in keeping customers satisfied.
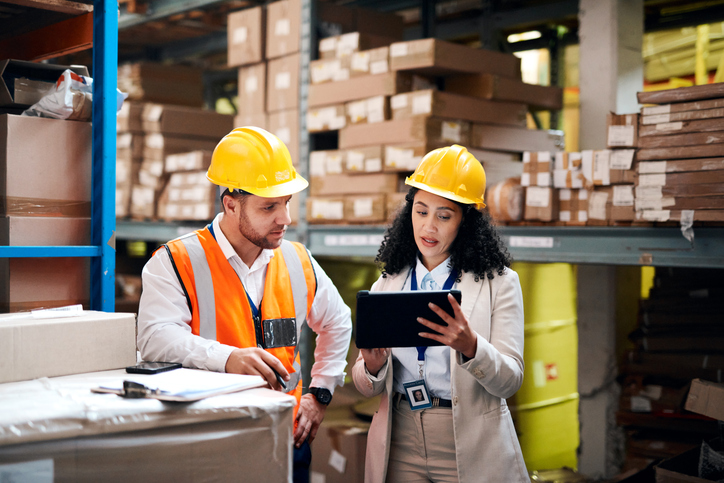
The fact that World Logistics Day has only existed for six years reflects how often the critical department goes unrecognized. Facilities managers know how that feels. Though World FM Day (May 8th) was introduced all the way back in 2008, both departments often find themselves relegated to obscure positions and regarded as cost centers. With computerized maintenance management system (CMMS) technology bridging the gaps between them and enhancing their capabilities, both departments can not only improve their results but also advance their roles within the organization.
CMMS Platforms Benefit Facilities and Logistics Departments
Donβt let the term βmaintenance managementβ convince you that CMMS technology only supports one department. In fact, it helps bridge the gap between departments by creating a single source of truth for real-time and historical data related to facilities, equipment, and vehicles. Breaking down information siloes and streamlining communication, a CMMS makes every internal stakeholder user more cross-functional, strategic, and informed.
Tech-Enabled Maintenance Management
Whatβs good for logistics departments is good for facilities managers. When organizations successfully implement and adopt platforms to transform their maintenance operations, they see a huge range of short- and long-term benefits.
- More proactive planning and scheduling: Automating preventive maintenance scheduling improves asset management across departments, helping keep budgets manageable and preventing unplanned downtime.
- Operational efficiency boosts: By refining processes and optimizing resource allocation, a CMMS enables data-driven decisions to make the entire organization more efficient and agile.
- Optimized parts inventory management: Data on usage trends and parts availability enable logistics and facilities departments alike to avoid the costs associated with last-minute orders and keep essential equipment operational.
- Improved safety and compliance: Centralizing documents and streamlining review processes makes it simpler and less stressful to both set and enforce new safety protocols for operators, technicians, and drivers.
- Enhanced reporting: Customizable dashboards for developing and delivering reports on key metrics help both departments to collaborate in meeting organizational goals. New insights into asset health allow for more proactive repairs and improved routes while insights into employee performance drive accountability.
- A culture of continuous improvement: Access to comprehensive reports encourages a sense of ownership and investment, driving facilities and logistics departments to continue setting new standards. Thanks to the results enabled by your CMMS, these teams will inspire other departments to drive innovations of their own.
These benefits to logistics and facilities management are just one component of the holistic transformation a world-class CMMS can enable. Optimizing maintenance with technology drives improvements across the full supply chain, improving vendor relationships and empowering businesses to continue offering the high-quality products and services customers expect.
Bryan Christiansen is the founder and CEO ofΒ Limble CMMS. Limble is a modern, easy-to-use mobile CMMS software that takes the stress and chaos out of maintenance by helping managers organize, automate, and streamline their maintenance operations.
The post Bringing Facilities Management and Logistics Together with a CMMS appeared first on Facilities Management Advisor.