What Facilities Managers Need to Know About Tracking Warranties
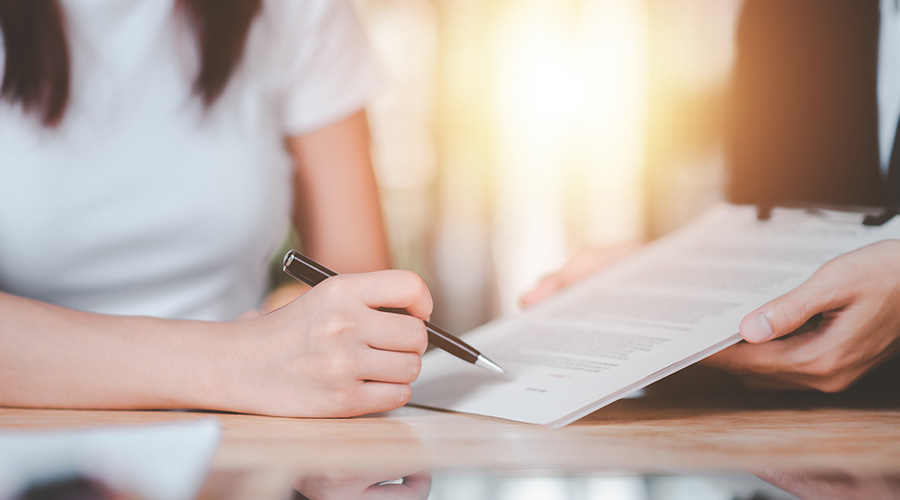
It doesn’t matter what industry it is; money will always talk. In facilities management, budgeting for equipment is a crucial part of the job. Fortunately, many pieces of equipment are protected by warranties, however, this can be difficult to track and manage on top of other everyday tasks. FacilitiesNet recently spoke with Andy Gager, CEO/President, AMG International Consulting and Kristian Byk, director of operations, Watchung Hills Regional High School on how managers can best manage their warranties.
FacilitiesNet: How do you integrate warranty tracking with other facility management processes?
Andy Gager: Maintenance Planners should have the ability to track and monitor warranty items along with planning any corrective work or scheduled work execution. If the item is flagged as repairable or under warranty, the maintenance planner should see that in the item master.
Kristian Byk: The first thing I do is any warranty information goes into a main file which is then shared with both my google calendar and facilities work order system.
FacilitiesNet: What information do you typically include in your warranty records?
Gager: Date of installation, current maintenance plans, service records, failure history
Byk: The information I include is make, model, serial number – for any and all new equipment and/or time of purchase, accompanied by the warranty contract and expiration date.
FacilitiesNet: How do you track the performance and reliability of products under warranty
Gager: Equipment Maintenance Plans (EMP’s) or Asset Management Plans (AMP). These plans include all the PM’s & Predictive activities on that asset. Work Order management, capturing history of work completed including any corrective maintenance performed. We can calculate the probability of failure, failure rate, and Mean-Time-Between-Failures (MTBF) & Mean-Time-Between-Maintenance (MTBM). Implement RCM principles to identify the failure patterns of components or if the consequence of failure to too great of a risk, then perform a Failure Modes & Effects Analysis (FMEA/FMECA) to refine the current maintenance strategies to mitigate or eliminate the failure
Byk: We track the performance and reliability of any products under warranty both through our work order system, our preventive maintenance system, maintenance contracts, and energy savings plans.
FacilitiesNet: Are there specific tools or resources you would recommend for tracking warranties?
Gager: Several CMMS have the feature to upload warranty documents and reminders. There also many software apps to track warranties. But the simplest method is to use the calendar and set-up reminders.
Byk: The best practices for maintaining accurate and up-to-date warranty records is through our maintenance facilities software system which helps communicate and expedite any maintenance and warranty issues. For tracking warranties and resources, I would recommend having a solid facilities work order and maintenance system as well as sharing any and all information on a google drive which helps keep communication on all levels current. I can’t stress this enough, have a firm and solid facilities management software for both work orders, preventive maintenance that includes as much information on both the warranties and proper service requirement intervals. Upfront it’s a lot of work to input all the data, however, what it will save you long term is worth more than gold. The other thing I’d like to stress is communication and sharing of information throughout all levels of the facility. This is key to expediting work orders, repairs, and routine maintenance.
By Mackenna Moralez, Associate Editor
Mackenna Moralez is the associate editor for the facilities market.
The post "What Facilities Managers Need to Know About Tracking Warranties" appeared first on FN Prime Maintenance & Operations