Making the Case for Metal Roofs
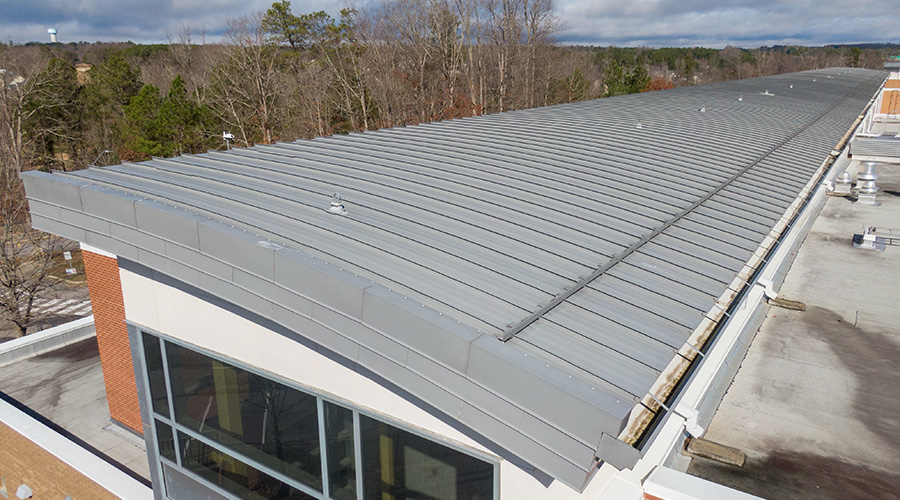
Managers see benefits through fewer replacements, improved sustainability.
Despite the availability and popularity of metal roofs, shingled roofs remain the more popular choice for many commercial building owners and facility managers due to their cheaper upfront costs.
However, being aware of the inherent advantages of a metal roof will quickly change this perception. With its durability, energy efficiency and minimal maintenance requirements, metal roofing quickly pays for itself, says Richard Off, senior architect for Hoffmann Architects + Engineers.
Off’s specialty is historic building restorations, where façade systems, roofing systems and windows are often a concern. In a recent New York restoration project, the firm replaced the batten-seam copper roof of an 80,000-square-foot university building.
Though Off admits most commercial building roofing projects do not involve copper for historic preservation purposes, he suggests there are many advantages to selecting a metal roof. The greatest of which is the resiliency and durability of the material.
“One of the biggest reasons to choose a metal roof is longevity. There are metal roofs in Europe, especially copper roofs, which date back to the Middle Ages,” he says. “In Philadelphia, there are metal roofs as old as the 1700s.”
In contrast, a shingled roof must be replaced every 15-30 years, with the exact timeframe dependent on shingle quality.
“If you opt for a metal roof, chances are it will be there for as long as you live, own or work in the building. A metal roof is a roof for life,” he says.
Consider the slope
Most roofs fall into one of two groups: Hydrostatic roofs, also called low-slope roofs, and hydrokinetic roofs, steep-slope roofs.
“The fundamental difference between the two is how they shed water,” says Bob Zabcik, technical director for the Metal Construction Association (MCA). “A hydrostatic roof must be tested and built in a way to withhold ponded water, whereas a hydrokinetic roof is designed and built to keep water moving across the roof surface, so it doesn’t intrude in the building.”
Both roof types can benefit from metal construction, Zabcik maintains.
“Metal is not the material of choice for a completely flat roof. There needs to be some slope for a roof to be done in metal,” Jeff Henry, MCA executive director says.
Off recommends having a roofing contractor field verify the roof to determine if it has enough slope to accommodate a metal roof, as many roofs considered “flat” actually have a slight slope and a flat seam system fully sealed may be possible depending on the configuration.
A snow guard or fence system is also necessary for steep-slope roofs in snowy regions, Off adds.
“When a metal roof gets warm, snow will slide off of it,” he says. “You don’t want massive piles of snow falling off in areas where people are walking or have their cars parked. You also want to protect roof drainage systems, because metal roofs typically rely on gutters versus internal drains. You don’t want those gutters blocked off or clogged up by extensive snow and ice.”
Pick a metal
Metal roofs are sustainable and durable because they are made from recycled and recyclable materials, Zabcik adds. The materials used for metal roofs include:
Galvanized steel: One of the most common types of metal roofing, this material comes in a variety of styles and color options. Galvanized steel can last over 40 years. However, it can be more susceptible to corrosion than copper.
Aluminum: Both versatile and affordable, aluminum roofing material also comes in many color options. The panels are lighter than steel, which makes them easier to install and less expensive to manufacture. On the downside, the material doesn’t last as long as steel and may need more maintenance.
Copper: This material is popular because it resists rust and corrosion and can last a lifetime. Copper also develops a patina over time, making it a striking element of building design. The catch is that this material is super expensive, so it’s not a practical option on many commercial buildings.
Each roof material also has specific applications, adds Off. For historic roof repairs or replacements, copper is the recommended material, but for building owners looking to save money, aluminum or steel are cheaper alternatives.
“The biggest thing to consider when choosing steel is how it’s treated, and where the building is located,” he says. “If it’s in a coastal area near a body of salt water, steel may corrode more rapidly than aluminum, which is naturally corrosion resistant.”
He also recommends applying a protective coating, to make the material more resistant to corrosion.
“Most people dislike the mil finish of steel, so they put a powder coating on it already,” Off says. “A fluoropolymer powder coating comes in a variety of colors and will help protect the metal and increase its service life. There are also high-end coatings and installation techniques that can maximize the coating longevity. There is concern that if the coating is not maintained and deteriorates, the metal will be exposed. And if steel is exposed, it will corrode.”
Besides coating it, steel can also undergo galvanization, which involves hot dipping it in zinc to prevent corrosion. There is also Galvalume steel, which coats steel with aluminum and zinc to increase its corrosion resistance.
“The most popular product in terms of market share is galvanized steel,” Henry adds. “But I also see a fair amount of aluminum and copper, which forms its own protective coating as it oxidizes.”
Ronnie Wendt is a freelance writer based in Minocqua, Wisconsin.
Related Topics:
The post "Making the Case for Metal Roofs" appeared first on Building Operating & Management