6 Tips to Keep Your Facility Safe
Although 96% of employees think physical safety is a top priority, they’re not sure their employers feel the same way. In fact, most workers overwhelmingly believe their employers put their reputation, productivity, and the bottom line above workplace safety. If a safety incident arises, many workers could be unprepared.
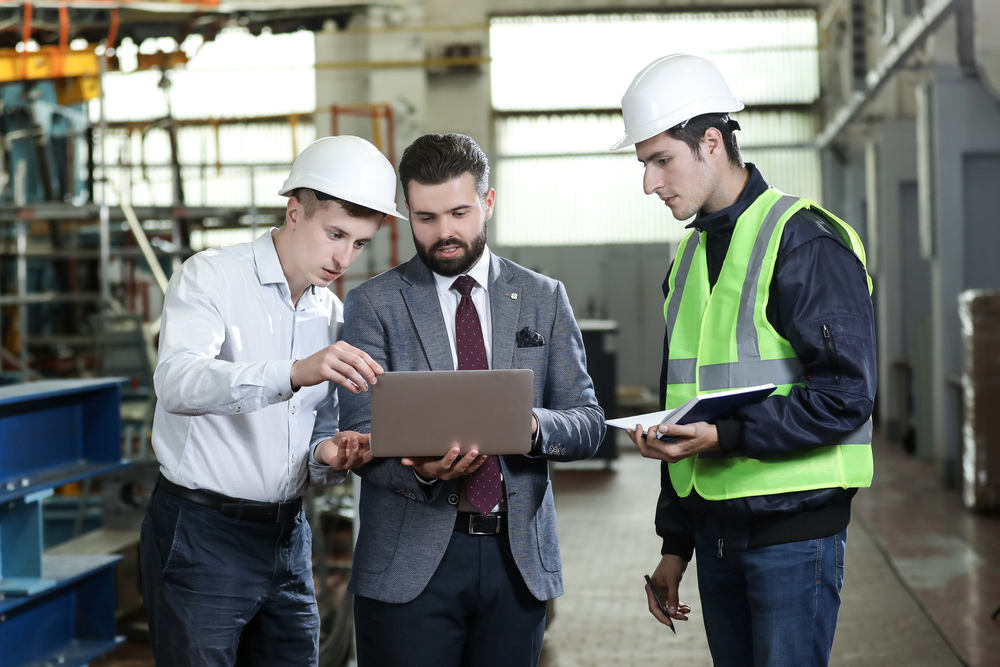
You can’t control when an emergency might happen. But you can control the quality of your safety program, from the training you provide to the incident reporting tools available. In this article, I’ll share six tips that can help you refresh your safety program and keep your facility secure.
1. Conduct a Thorough Risk Assessment (and Regular Safety Audits)
To keep your facility and workforce safe, you must know which hazards you’re guarding against. That’s why it’s important to carve out time for a thorough risk assessment. Do a careful walkthrough around your work environment, checking for things like:
- Hazardous chemicals: The Hazard Communication standard requires proper labeling, tracking, and employee training to mitigate risks associated with exposure to dangerous substances.
- Poor air quality: If your industry deals with dust, fumes, or chemical exposure, it’s absolutely crucial to ensure proper ventilation and personal protective equipment (PPE).
- Electrical hazards: Wiring and flexible cords can become fire or shock hazards if improperly installed or maintained.
- Inadequate machine guarding: OSHA requires certain pieces of equipment (such as physical barriers, light curtains, and two-hand trip devices) to have safety mechanisms in place to prevent injuries.
- Lockout/tagout failures: Following OSHA’s Lockout/Tagout standard, equipment should always be properly shut down and isolated from hazardous energy sources before maintenance.
Of course, workplace hazards aren’t always obvious—and neither are they static. Equipment can wear down. New machinery might be introduced. And new hazards could crop up over time. So on top of your initial risk assessment, make sure to schedule regular safety audits and inspections. This way, you can more easily monitor the biggest risks in your workplace—and prevent costly safety incidents.
2. Establish Clear Emergency Procedures
Whether you’re dealing with an electrical fire or a serious chemical spill, your emergency response can make or break your team’s safety. Make sure your facility has:
- A well-communicated emergency response plan that all employees understand.
- Clearly marked emergency exits and evacuation routes.
- Readily accessible emergency equipment (e.g., fire extinguishers, first aid kits, etc.).
- Regular drills for fire, chemical spills, and other potential emergencies.
With adequate planning, training, and equipment, your team can respond to emergencies faster and minimize disruption.
3. Invest in Safety Training and Regular Safety Meetings
Over 50% of employees say they don’t feel completely safe at work right now. The top two reasons: poor communication and inadequate safety training.
To maximize workplace safety, workers need to have clear and consistent safety training that shows them how to protect themselves and their team. To strengthen your current offering, make sure each training is:
- Relevant: Workers should be trained on the hazards and best practices relevant to their roles.
- Updated: Training should be refreshed periodically to incorporate new regulations and emerging risks.
- Practical: Hands-on demonstrations and role-playing exercises reinforce learning.
- Engaging: You can improve retention by incorporating real-world case studies, quizzes, and multiple forms of media (like photos and videos).
- Documented: Keep records of completed training sessions to ensure compliance and track progress.
Another recommendation? Supplement more comprehensive training sessions with regular safety meetings. These are different from “toolbox talks” (i.e., more informal, daily or weekly safety refreshers); they’re typically longer, more structured, and more spread out throughout the year (e.g., monthly or quarterly).
To run safety meetings effectively, I suggest focusing on a single topic for 20 to 45 minutes. Otherwise, you can approach them just like you would a typical training session. And remember to document everything—no matter how short or informal the conversation.
Whether it’s an in-depth training or a quick safety meeting, mobile EHS software can help a lot. I recommend looking for a platform that makes it easy for employees to progress through digital modules at their own pace and simplifies all the administrative work in an intuitive, cloud-based platform. The likely impact: greater employee engagement and less headache for your team of safety professionals.
4. Encourage Incident Reporting and Follow-up
Even with the best safety training curriculum, near-misses and incidents do happen. It’s crucial to stay abreast of them as they occur; a string of near misses, for instance, could signal that a larger problem is afoot.
Your team can help you spot these issues—but only if they feel empowered to report safety concerns without fear of retaliation. In practice, that means providing:
- Easy-access reporting (ideally via a mobile EHS app).
- Prompt investigations for every reported incident.
- Swift corrective action to prevent future occurrences.
As reports come in, regularly analyze trends to identify recurring hazards and high-risk hotspots throughout your facility.
5. Keep Accurate Safety Records
In many industries, safety professionals still rely on a hodgepodge of digital and paper-based systems to manage their safety records, which can easily result in inaccuracies over time.
You can modernize your operation with a streamlined digital platform for record keeping. Ideally, the platform you choose will let you:
- Track safety training completion and certifications automatically.
- Store incident reports in a central repository.
- Simplify inspections and audits with automated reminders and fillable forms.
With mobile software, you can handle all these activities on the go—a huge value add when you’re on site and away from your laptop.
6. Stay up to Date on Safety Regulations
As a safety professional, you know that regulations are constantly in flux—and effective compliance depends on staying informed. Keep up with the latest changes by:
- Subscribing to OSHA, ANSI, and other regulatory updates.
- Attending industry conferences and workshops.
- Partnering with safety consultants to audit and update your safety program.
As you learn of regulatory changes, share relevant updates in company-wide safety meetings to ensure all employees understand any new requirements.
Your Safety Culture Needs All Hands on Deck
All the tips I’ve shared so far will go a long way toward improving safety in your workplace. But to foster a true safety culture, you’ll need everyone’s investment, from the front line to the C-suite.
My recommendation? Encourage supervisors to set an example by modeling the safe behavior they want to see. Keep an open dialogue about safety that prioritizes honest conversation, not finger pointing. And remind workers just how committed you are to safety at every level of your organization.
Building a safety culture is an ongoing process, but the payoff will be huge: fewer incidents, stronger compliance, and a happier team.
Glorianna L. Reeser is a senior risk management consultant at KPA. She is among KPA’s team of environment, health, and safety (EHS) risk management consultants who work with clients auditing workplace conditions and safety programs, leading on-site EHS compliance training and safety committee meetings, and assisting with the management, tracking, and reporting of EHS issues.
The post 6 Tips to Keep Your Facility Safe appeared first on Facilities Management Advisor.