Facility Construction: 4 Steps to More Sustainable Projects
Facilities managers must feel like they’re balancing several seemingly conflicting pressures. Chief among them: budgets. Every dollar counts, and pressures on both the supply chain and labor markets leave little room for unexpected cost premiums. At the same time, the incentives for more energy and water efficiency—and the long-term bottom line benefits they can unlock—are appealing, especially for organizations that have committed to carbon reduction goals. However, looking at those factors at the wrong time in the construction and design process has the potential to add cost.
It’s an unenviable position for anyone planning facility renovations or new ground-up facilities. Fortunately, facilities managers can tap in to best practices of design and building strategies specifically aimed at enabling higher building performance as pen hits paper on design. The upshot is, while traditional strategies that enable things like higher-efficiency fixtures and more are still valid, the right kinds of early planning can unlock even more value and building performance, all while lowering carbon.
Attention to three specific areas during project planning and one during project work not only help deliver higher performance and lower environmental footprints, but also help facilities managers demonstrate the value of their recommendations to other stakeholders.
1. Identify What Can Really Be Reused
Recently, I was part of a renovation project where the initial plan was to reuse the existing building’s skin. On paper, this was a great idea and would have huge savings on embodied carbon; you don’t have additional embodied carbon on reused materials, after all. However, during the deconstruction process, the team discovered too much damage to the existing skin. The result was millions of dollars’ worth of risk, as the team had to replace it with new glazing and other materials.
For a facilities manager, that’s a tough conversation to have. So, before a project can truly be conceptualized, facilities managers should conduct thorough inspections of their portfolios for reusability. Taking this deep dive can give a clear picture of what materials can be reused in renovations, which in turn will lower embodied carbon for lower cost and allow for more focus on driving energy use intensity improvements.
That information can help drive decisions at the earliest project phases, informing design and construction strategies. This sort of data can put project teams on the same page and help create design and construction plans based on the owner’s goals and the state of play with the facility. It’s like how if you know a major highway is closed, you plan ahead to take a different route rather than discovering the closure on the way and losing hours of time and energy backtracking to find a new path.
2. Planning for Energy Use Intensity
Armed with materials reuse knowledge, project teams are now able to make informed recommendations on ways to reduce a facility’s overall energy use intensity. Teams working within known conditions can realistically evaluate how sealed the building envelope is and identify materials and systems that are best-fit for the space. That can help inform the most appropriate HVAC and MEP systems for the space and even the suitability to offset the energy load with on-site generation methods. In many areas, it’s worth doing a similar evaluation for water use and seeing if rainwater collection, greywater use, and more can lower water footprints.
Also, a pattern should emerge: Making the best possible decisions comes with design and construction partners at the table early. Whatever delivery method you choose for your projects, including those voices from the start and working toward shared goals has shown time and again to yield the highest-performing buildings. The change in traditional workflows can be initially challenging, but it is notable that once a project team starts using more collaborative delivery methods, it is very unusual for them to switch back to the linear design-bid-build process that has been the norm for centuries.
Working together in this way, the team can apply the combined knowledge from thousands of projects to surface environmental solutions that can otherwise be overlooked.
Properly planned for, the team can take big swings to cut down energy, water, and carbon footprints inherent to the building before decisions like which fixtures and finishes will be most efficient. By choosing “system” (in this case, the building itself) rather than just “point” solutions (e.g., lower-energy fixtures), facilities teams can take a bigger bite out of environmental footprints.
3. Adopting a Programmatic Approach
Very few facilities managers are responsible for just one building. More frequently, facilities teams are managing a number of spaces and even entire campuses or assets around the nation (or world).
Especially for organizations with major carbon and climate commitments, taking a programmatic approach to increasing sustainability not only makes good sense as a big-picture strategy, but it can create project-by-project efficiencies.
By their nature, renovations are usually in response to changing market conditions, end user trends, and advancements in technology. A key consideration is evaluating how those will manifest and designing spaces to be as flexible as possible, especially with an eye to what can be reused in the future. Since reuse means not sourcing, manufacturing, and transporting new materials—and their carbon footprints—the greenest buildings are the ones you find ways to renovate and find new uses for existing elements and fixtures. This upfront planning stage is also a great time to focus on health and wellness factors for occupants. It’s vital to create high-performing buildings that offer a nourishing environment for health and wellness. Design, planning, and procuring these materials takes early integration for a streamlined approach that combines budget, schedule programming, and impact.
Individual portfolio needs will differ, but it is critical for project teams to understand those needs prior to design and construction. Identifying the right materials that are needed can also create economies of scale, potentially allowing for lower costs, streamlined shipping—which lowers embodied carbon—and create operational efficiency by making sure critical or defining elements of each facility are consistent, a benefit for operations and maintenance.
4. Advanced Commissioning and Data Utilization
Facilities managers also know that there is no such thing as a set-it-and-forget-it building. In fact, for builders in the sustainable space, few things are as much of a downer as seeing a well-designed and -built facility not perform as planned. It’s like buying a Ferrari, but only driving it to and from the grocery store and, perhaps, never changing the car’s oil.
The work to ensure performance has to start during construction with advanced commissioning to ensure systems are operating as designed and built so that facilities managers have all the knowledge to operate the systems effectively. Energy, water, and air quality systems should all be included. Building occupants should also be educated on the ways they can contribute to making sure the building operates as best as it can, whether it’s from explaining fresh air ventilation and daylighting systems to understanding how they affect plug loads.
Once operational, maintenance is a given. However, like today’s cars, advanced metering can provide an “under the hood” look at building performance, helping identify lagging areas or places that need attention before a major issue arises.
An upshot of gathering all of this data is, after several months of operations, facilities teams should begin to have data that—if everything is operating as it should—help them demonstrate ROI to other stakeholders, helping facilities managers show the true business impact of the decisions made early on in the process. As carbon reporting regulations arise, that information will be nearby, as well.
Ironically, all of these approaches can feel separate from the design and construction process on paper. Consider that when we watch sports, we see the game—and that is obviously where much of the action takes place—but we don’t always see the planning for the game: learning from previous experience and film, determining a game plan, practicing that game plan, and adjusting. You cannot separate those elements from the game, and you must include all players throughout the process if you want success. In construction, it’s the same.
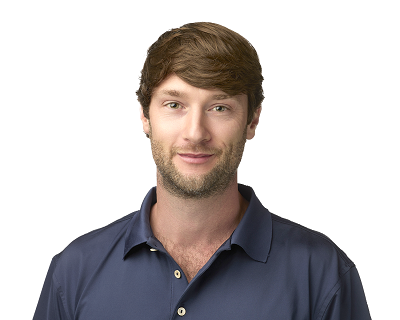
Ryan Poole is a sustainability leader at technical builder DPR Construction.
The post Facility Construction: 4 Steps to More Sustainable Projects appeared first on Facilities Management Advisor.