How to Create Easy-to-Use Preventive Maintenance Checklists
Preventive maintenance (PM) checklists are essential tools in the effective management of building maintenance and facility equipment. Their primary purpose is to methodically guide maintenance tasks, ensuring that all necessary steps are performed in a timely and consistent manner.
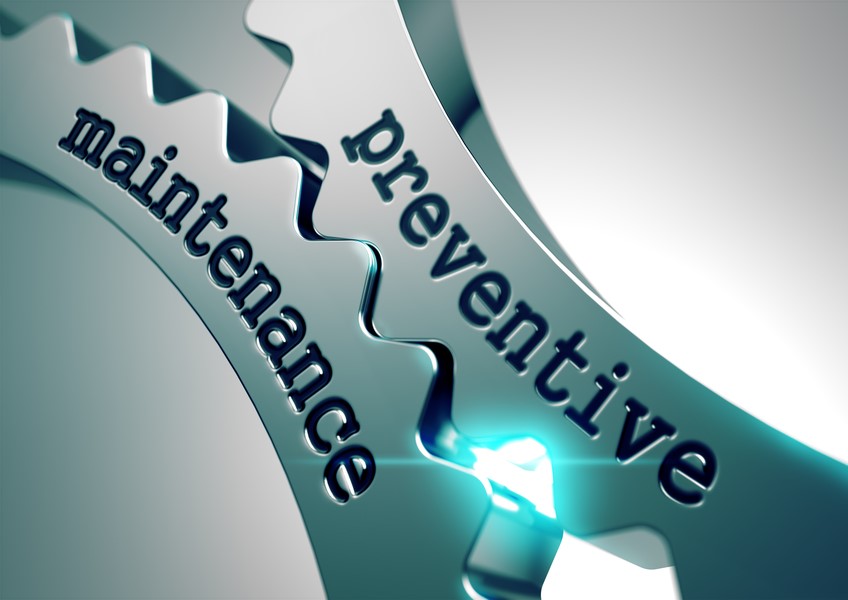
Let’s dive straight into essential elements and best design practice to discover how to create clear and effective PM checklists that are easy to follow.
Key Components of an Effective PM Checklist
There isn’t a universal rule on what must be included on each PM checklist. However, most will, in one shape or the other, contain the following details:
- Identification details: Specifics like equipment name, model, location, and ID number to ensure precise tracking and maintenance of each asset.
- List of required resources: List of tools and spare parts needed to complete the task at hand.
- Safety precautions: The necessary safety measures and personal protective equipment requirements, prioritizing the safety of maintenance personnel.
- The actual steps to be performed: List of sequential steps a technician should follow while performing the scheduled inspection or assessment.
- Record-keeping section: A space for recording maintenance dates, technician names, and any observations or issues encountered, fostering accountability and historical data tracking.
- Sign-off field: A sign-off section for technicians to confirm the completion of tasks, ensuring accountability and task completion tracking.
- Additional resources: Attachments like relevant equipment manuals and visual aids.
Each type of equipment, from HVAC systems to industrial machinery, has specific maintenance requirements and operational nuances. Customized checklists ensure that specific maintenance protocols are followed, and they also aid in training new technicians by providing clear, equipment-specific guidelines.
Designing the Checklist for Clarity and Ease of Use
Designing a PM checklist involves creating a document that is intuitive and easy to navigate, without missing any key information.
1. Create a User-Friendly Layout
Creating a user-friendly layout for a PM checklist hinges on your design choices. Most facilities managers will either use a Computerized Maintenance Management System (CMMS) or a standalone tool for building online forms and checklists.
In any case, you will want to use clear, legible fonts and organize information in a logical flow, such as grouping related tasks together. Utilize yes/no fields and checkboxes for task completion, as well as color coding for different task categories or priority levels.
Additionally, ensure that the layout is consistent throughout the document to help users quickly become familiar with the format—which then can be used as a template when building other PM checklists.
2. Use Clear and Concise Language
Using clear and concise language in PM checklists is crucial for effective communication. It ensures that tasks are easily understood and followed, reducing the risk of misinterpretation and costly errors.
For instance, use active voice (“Inspect the air filter” instead of “The air filter should be inspected”) and avoid technical jargon unless necessary.
Furthermore, be precise in instructions; for example, say “Check the coolant level and refill if below the marked line” rather than just “Check coolant.”
Lastly, if there is a step that just can’t be described in a simple manner, consider breaking it up into multiple steps.
3. Outline Steps in Sequential Order
This step ensures that tasks are completed in a logical and efficient manner. Sequential steps also help prevent crucial steps from being overlooked and ensure that maintenance procedures align with the designed operational flow of the equipment.
While outlining the steps, don’t blindly stick to original equipment manufacturer (OEM) guidelines. Adjust the process to account for past equipment failures and its operating environment. This is why it is important that a checklist is built (or at least approved by) an experienced technician that knows the asset in and out.
4. When Needed, Include Visual Aids
Visual aids are especially important for complex tasks or those with inherent safety risks. Annotated pictures or equipment schematics can provide clear, visual instructions that are easier to follow than text alone.
For instance, a checklist for electrical equipment maintenance might include a schematic diagram to identify parts safely, or an instructional video could be linked for a complex calibration process.
The visuals can also include specifics such as location maps, diagrams of machines with all lubrication points clearly marked, key areas prone to leaks or blockages, or short videos demonstrating proper inspection techniques.
Incorporating Digital Tools and Technology
The shift from traditional paper checklists to digital forms offers enhanced accessibility, allowing technicians to access and update task status in real time from any location. Digital forms also enable better data organization and analysis, providing insights into maintenance trends and equipment performance.
Various software and applications are available for creating and managing digital PM checklists. A CMMS is often a go-to solution in order to keep all of the maintenance documentation and data stored within a single platform.
However, organizations that do not use maintenance software will often find it easier to search online for a no-code solution for building mobile forms. These apps streamline the checklist creation process, offering customizable templates, sharing options, and the ability to use the form off-line (with automatic syncing when the mobile device reconnects to the internet).
When going down the latter route, make sure that your mobile form builder can integrate with any existing facilities management system you might be using. Such integration ensures that maintenance schedules, inventory management, and work order tracking are all aligned and up to date.
Set It, but Don’t Forget It!
As equipment ages or facility operations evolve, the maintenance requirements can change. Periodically review your PM checklists to make sure they are up-to-date to maintain operational efficiency and safety.
Facilities managers should view these checklists as dynamic tools, continually evolving with their facilities’ needs. Dedicating effort to this aspect of maintenance significantly impacts the reliability and efficiency of their operations, especially when these checklists become widely used and relied upon.
Kendall Kunz is the founder and CEO of Forms On Fire, a mobile forms automation platform.
The post How to Create Easy-to-Use Preventive Maintenance Checklists appeared first on Facilities Management Advisor.