Improve Maintenance With Acoustic Imaging
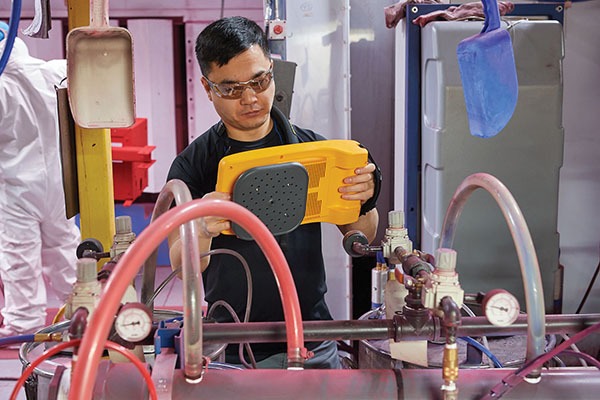
For more than a decade, the Univ. of Tennessee Reliability and Maintainability Center (RMC) has been using Fluke, Everett, WA (fluke.com) technologies to demonstrate, test, and learn various applications. The most recent application of interest and promise has been acoustic imaging. I’ve invited Fluke specialist, Justin Sheard (Principal Engineer for New Product Solutions), to provide further details.
Acoustic-imaging technology has emerged as a transformative tool in various industries, offering a novel approach to sound analysis. It provides precise visual representations of sound sources, contributing significantly to industrial maintenance, enhancing reliability, and ensuring safety.
Understanding
Acoustic-imaging technology excels at converting sound waves into precise visual data. The process involves several key steps:
Sound-wave capture: Sensitive microphones or sensors are strategically placed to detect sound from different directions, registering variations in timing and intensity.
Data collection: These sensors record sound attributes such as frequency, intensity, and detection time, transmitting the data to a central processing unit.
Data processing: Advanced algorithms analyze the data, determining the precise source location by comparing time delays and sound intensities.
Visual representation: Processed data is presented visually, often as a “sound map” or “sound image,” displaying sound sources and intensity through color coding or shades.
User interface: Users interact with the visual representation, enabling precise identification and analysis of sound sources.
Industrial Applications
Acoustic imaging technology finds robust applications in industrial settings, enhancing maintenance and reliability. These include, but are not limited to, leak detection, machinery monitoring, electrical partial-discharge detection, and optimizing compressed air and gas systems.
Leak detection is a critical application of acoustic imaging technology. It involves identifying gas or air leaks in pipelines, compressed-air systems, and industrial equipment. By pinpointing the exact location of leaks, this technology minimizes downtime and enhances safety.
Machinery monitoring is another vital industrial application. Acoustic imaging helps identify mechanical issues in rotating machinery, conveyors, and production lines. By detecting anomalies early, it prevents costly breakdowns and ensures the smooth operation of essential equipment.
In the electrical industry, acoustic-imaging technology is used to detect electrical partial discharge. This is crucial for high-voltage equipment.
Acoustic imaging also plays a pivotal role in optimizing compressed-air systems. It maximizes capacity and reduces energy costs by precisely pinpointing leaks. Additionally, it provides visual evidence that supports repair decisions, ensuring the efficiency of these critical systems.
Benefits
Acoustic imaging technology offers several significant benefits when applied in industrial settings. These advantages include:
Early anomaly detection: Acoustic imaging enables the early detection of issues such as leaks or mechanical wear.
Non-intrusive inspection: A notable advantage is that acoustic imaging does not require physical contact with equipment. This reduces the risk of damage to machinery and minimizes downtime.
Increased safety: Acoustic imaging can take place a safe distance from moving machinery and out-of-reach or otherwise dangerous scenarios. Inspections can occur from distances to 50 meters.
Improved efficiency: One of the primary benefits is the streamlining of maintenance processes. Acoustic imaging reduces troubleshooting time and increases overall productivity.
Cost reduction: Detecting and addressing problems early in the maintenance cycle leads to substantial cost savings. These savings encompass maintenance expenses, repair costs, and energy consumption reductions, not to mention avoiding costs associated with lost production.
Data visualization: Acoustic imaging provides visual representations of sound sources and anomalies. This visual data enhances decision-making and communication among maintenance teams, operators, and management.
User friendly: Personnel without specialized expertise can effectively operate these systems with minimal training.
Real-World Examples
The technology has already made significant contributions to various industries:
Leak detection in petrochemical plants: Acoustic-imaging technology has revolutionized leak detection in petrochemical plants during turnarounds (TAR), which involve maintenance, equipment installation, and inspections. TAR periods are susceptible to risks such as fires and explosions. Acoustic imagers use an array of highly sensitive microphones to capture audible and ultrasonic sound ranges. These images provide a color-coded spectrum of sound levels by frequency,
enabling the visualization of leaks, even in noisy environments. This technology enhances safety and efficiency during TAR operations.
Efficient conveyor maintenance: In food-production, logistics, and mining industries, conveyor systems are critical for operations. Precision acoustic imagers with advanced modes are used for proactive conveyor maintenance. They detect unusual sounds generated by mechanical components, helping identify potential issues early. By targeting unhealthy conveyor bearings, the technology reduces energy consumption, prevents downtime, and lowers maintenance costs.
Compressed-gas leak detection in healthcare: Healthcare facilities must ensure the safety of patients and employees around compressed-gas systems. Acoustic imaging cameras offer non-intrusive and safe leak-detection methods. They have been used to swiftly identify and resolve compressed-gas leaks, even in busy environments. This technology enhances patient and employee safety, ensures regulatory compliance, and minimizes the risk of accidents.
Optimizing compressed-air systems: Many industries rely on compressed-air systems. Leaks in these systems can lead to energy waste and increased operational costs. Companies use acoustic-imaging technology to optimize existing systems and identify leaks that limit capacity. Acoustic imagers help pinpoint leaks and provide visual evidence, making it easier to convince customers of the need for repairs.
With its ability to provide precise visual representations of sound sources, this technology has become an invaluable asset in industrial maintenance and reliability. As it evolves, it will play an increasingly pivotal role in shaping the future of industrial maintenance and industrial processes.
By Dr. Klaus M. Blache, Univ. of Tennessee Reliability and Maintainability Center (RMC), and Justin Sheard, Fluke
Based in Knoxville, Klaus M. Blache is director of the Reliability & Maintainability Center at the Univ. of Tennessee, and a research professor in the College of Engineering. Contact him at [email protected]. Justin Sheard is the Principal Engineer for New Product Solutions for Fluke, Everett, WA (fluke.com).
The post "Improve Maintenance With Acoustic Imaging" appeared first on Efficient Plant