Modular Construction: A Different Approach to Building Healthcare Facilities
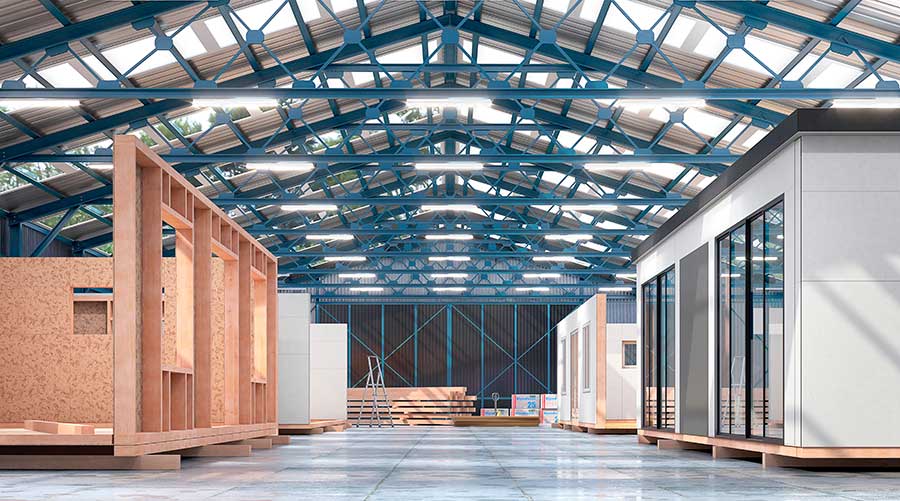
Constructing healthcare facilities is a lengthy process in and of itself. Within the process are hours of careful planning and designing, as the product must meet the expectations of patients and the public at large. Modular construction poses itself as an alternative approach to the traditional style. Healthcare Facilities Today recently spoke with Rita Lemley, vice president of modular interior construction at ForBuild, about modular construction and what it could mean for building healthcare facilities.
HFT: In what ways does the use of modular construction in healthcare facilities align with sustainability goals and environmental considerations?
Rita Lemley: We work with our clients to understand their sustainability goals and identify how building with prefabricated construction solutions can support LEED, WELL and Living Building Challenge. Our partner, DIRTT, calculates various materials and elements of the built environment that support certification. In addition to first build sustainability measurements, the system allows for repurposing your built environment, you protect your investment through future reconfigurations and relocations, while keeping waste out of the landfill. Our prefabricated systems are designed for disassembly to reduce the carbon footprint of new construction and future changes.
HFT: How does modular construction contribute to the efficiency and speed of building healthcare facilities?
Lemley: Our ForBuild construction team and prefabricated solutions can provide efficiency and speed from schematic design phase through construction. We are partners to the design team, owner and contractor to ensure a quality set of documents is prepared for the project, to educate and define the scope of our solutions and the impact on all trades. This efficiency transfers to the field with manufacturing happening while early construction phases are being completed on site. Our systems arrive on site just in time for quick assembly and connection to the base building.
HFT: Are there any limitations for design flexibility with modular construction?
Lemley: Prefabrication of interior building elements provides unlimited material options and details. The only limitation is the size of components that can be brought into the building. This would be the same challenge with conventional or prefabricated construction.
HFT: Are there any quality control challenges for modular construction with healthcare facilities?
Lemley: The quality of prefabricated construction is far superior to conventional onsite construction. The components and systems are built in a controlled manufacturing environment. The solutions go through a multi-point inspection for material quality control and inspections of finished assemblies. The assemblies are once again inspected when delivery arrives at our warehouse or job site.
Jeff Wardon, Jr. is the assistant editor for the facilities market.
The post "Modular Construction: A Different Approach to Building Healthcare Facilities" appeared first on Healthcare Facilities Today