The Importance of Workplace Safety in the Warehouse
Employers must implement workplace safety measures to protect the lives of their employees. Warehouse professionals must follow these measures as it is a matter of life and death. According to the Census of Fatal Occupational Injuries, there were more than 5,283 fatal work injuries in 2023.
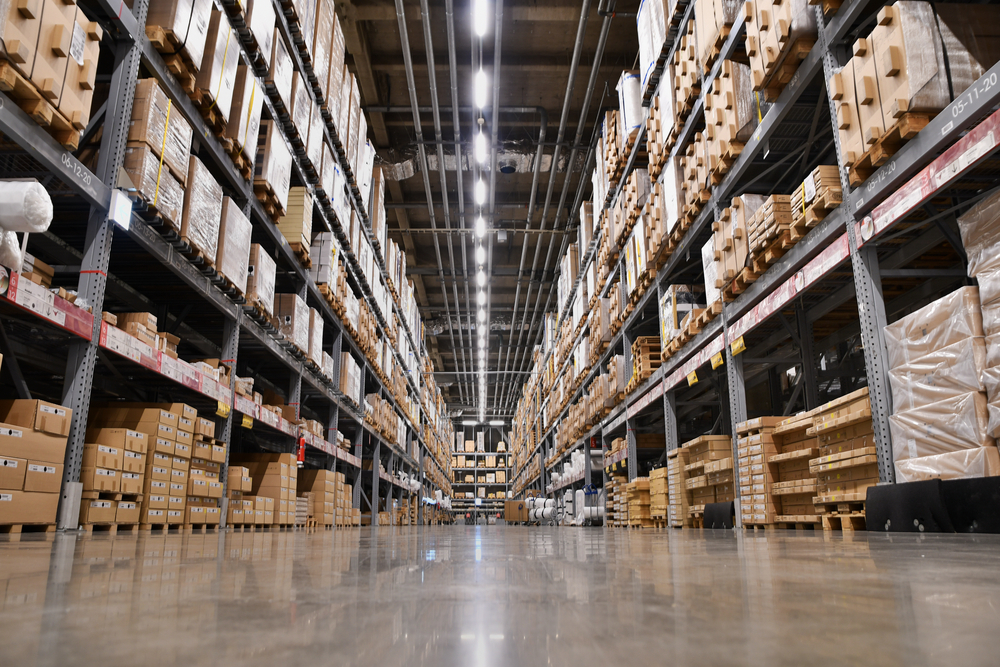
Warehouse professionals should wear proper protective clothing as a safety measure. For example, wear fireproof clothing when working in a fire-hazard environment.
This article discusses common warehouse hazards, strategies for implementing warehouse safety, and the senior manager’s role in ensuring warehouse safety.
Common Warehouse Hazards
According to the Occupational Safety and Health Administration (OSHA), warehouse workers face various hazards in their daily lives. A hazard is any potential source that can cause harm or illness. Ergonomic and musculoskeletal disorders are examples of hazards not commonly spoken about.
This hazard affects warehouse workers exposed to ergonomic risk factors such as repeatedly lowering and lifting heavy items. This causes muscle strains and carpal tunnel syndrome, a painful condition that occurs when the nerves in the wrists are compressed. Industry standards increasingly highlight the importance of investing in high-quality safety gear. Many employers prioritize products from American-made workwear brands, known for their focus on ergonomic design and durability, as part of broader efforts to enhance worker safety.
Other common warehouse hazards to know about include:
Physical Hazards
Physical hazards are the most common. They can cause serious injuries or death. Examples include slips, trips, and falls. They are caused by several factors, such as uneven floors, spilled liquids, or a cluttered workplace.
Physical hazards include heavy machinery, such as forklifts, that might tip over. Hazards also include risks associated with falling objects, especially if the items are stored on high shelves.
Hazardous Chemicals
This hazard affects warehouse professionals working in manufacturing, construction, and agriculture. In the manufacturing industry, professionals use chemicals directly to produce various products. This exposes them to hazards such as toxic fumes and lead.
Employers dealing with hazardous chemicals must abide by OSHA’s Hazard Communication Standard (HCS).
According to this standard, safety, and warehouse professionals must have a written hazard communication program for the warehouse. Managers must also train workers to identify and use hazardous chemicals.
Refrigerated Housing
Warehouse workers working in refrigerated storage facilities are usually affected by this hazard. An example is a meatpacker who works in cold rooms. Workers in these facilities experience cold stress or conditions such as hypothermia and frostbite.
Another type of hazard found in refrigeration facilities is exposure to ammonia. Refrigerated warehouses use anhydrous ammonia, which causes skin irritation. Similarly, ammonia can also ignite and cause fire.
Importance of Implementing Safety Measures
Creating and implementing various warehouse safety measures is crucial for legal and safety compliance. Safety measures help protect the well-being of warehouse workers from common hazards such as slips, falls, and equipment-related injuries.
In addition, safety measures enhance operations efficiency as operations run without downtime caused by work-related injuries. According to research by the National Library of Medicine, an injured worker takes around 45 days for an injured worker to return to work.
Implementing safety measures ensures compliance with various laws, avoiding legal penalties. These laws are based on organizations such as OSHA and the International Labor Organization.
An example is the OSH Act of 1970, which mandates employers to provide a workplace free from hazards that can cause death. OSHA standard CFR 29 1910 Subpart N creates guidelines for handling warehouse materials.
Lastly, implementing safety measures is a cost-effective strategy that protects the business from financial losses caused by accidents. Workplace accidents can result in lawsuits and increased insurance premiums.
A good example is when Judge Letty Lopez ordered the Hyster-Yale Group to pay a forklift operator $10.5 million. The operator had suffered a fractured leg due to a 2017 work-related injury that caused a total loss of mobility.
Best Practices for Enhancing Warehouse Safety
Creating a safe warehouse environment requires a proactive approach and commitment by senior management to foster a safety-first culture. Some of the best practices that foster warehouse safety are:
Conducting Regular Safety Training
Regular safety training helps warehouse workers identify potential hazards before they cause injuries. The training should be engaging and fun.
In addition, they should be relevant. For example, if the warehouse professional handles hazardous chemicals, the training should focus on the chemicals.
Using Clear Communication
Quick and reliable communication is vital in a busy warehouse environment. Using two-way radio helps workers share real-time updates about potential hazards, coordinate tasks, and call for immediate assistance if an emergency arises.
This ensures a faster response to safety concerns and fosters collaboration among team members, contributing to an overall safer and more efficient operation.
Use Proper Safety Equipment
Use proper safety equipment based on the specific hazard. For example, workwear such as steel-toe boots, hard hats, and anti-slip gloves are best for physical hazards.
Similarly, the best safety equipment for environmental hazards would be thermal-resistant clothing, protective masks, and weatherproof workwear.
Lastly, warehouse professionals must be aware of emergency safety procedures. These procedures should include evacuation plans in case of spills and fire. Safety systems such as fire alarm buttons and extinguishers should be marked and easily accessible.
Role of Management in Warehouse Safety
Management should play a key role in ensuring warehouse safety. They must foster a culture of safety and enforce policies that promote safety. Senior managers should lead by example.
They can do this by adhering to safety protocols and participating in safety training sessions. They should also create warehouse safety protocols, comprehensive guidelines on equipment use, and emergency response procedures. The procedures should be regularly updated and enforced.
Lastly, management should allocate resources for safety initiatives such as regular training and purchasing safer equipment.
Nick Warrick is the sales manager at All Seasons Uniforms. With over 15 years of experience in the work uniform business, he has worked with over 100 clients across 20 different industries.
The post The Importance of Workplace Safety in the Warehouse appeared first on Facilities Management Advisor.