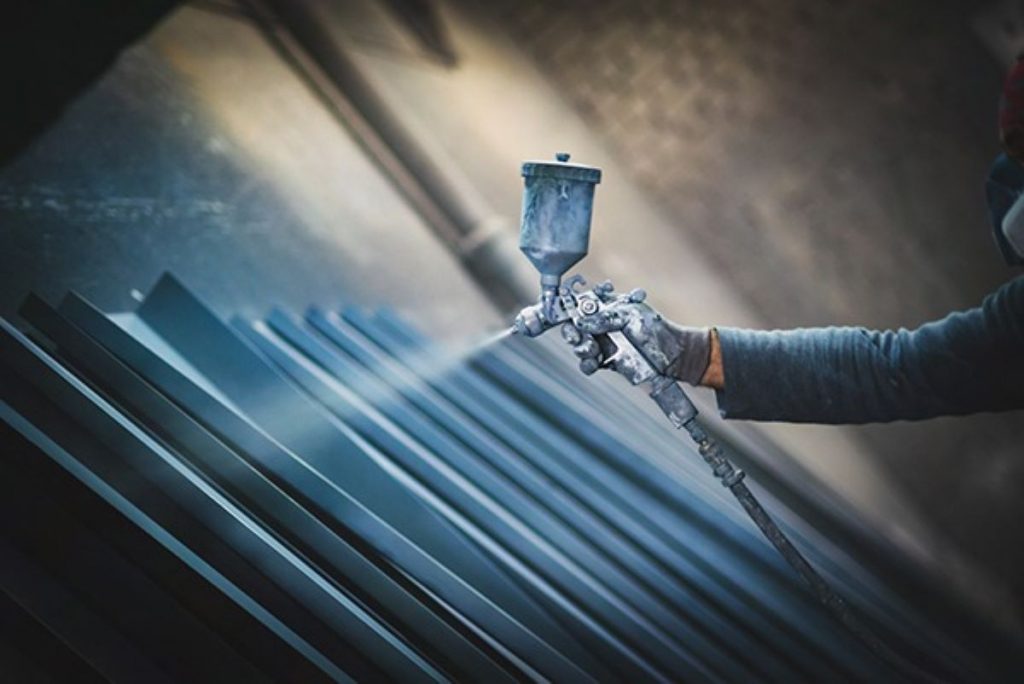
The heat that’s generated by your air-compression system can be used in a variety of ways.
Generating compressed air typically consumes as much as 10% of a plant’s total energy cost. This energy usage can be kept in check by patching leaks, regular maintenance, or by using capacity-control technology to help match air output with demand.
A significant beneficial component of compressing air is heat. As much as 93% of the energy required to compress air is converted to heat. This heat energy is typically dissipated into a compressor room where it adds no real value. By designing in and using efficiency- and heat-recovery tools in a compressed-air system, you can re-purpose extraneous heat to warm process water and provide facility heat, contributing to energy savings and sustainability benefits. The return on investment is typically as little as 3 to 5 yr.
Bringing the Heat
Rotary-screw air compressors are especially well-suited to heat recovery due to their operating principles and design. Both oil-flooded and oil-free compressors can lend themselves to effective heat recovery. In the case of flooded screw compressors, the heat of compression is transferred to the fluid injected into the compression chamber. This heat is then recovered from the fluid, using a number of techniques. Additional heat can be recovered from the compressed air itself.
In an oil-free compressor, the heat of compression is contained within the compressed air. Due to the higher operating temperatures of an oil-free compressor, as well as piping considerations, heat recovery within can be more challenging and require more investment.
Applications Abound
Applications for the rotary-screw compressor’s heat byproduct are many. Each offers unique savings opportunities, as well as installation considerations and investment. One use is for pre-heated make-up air. This solution is applicable to an air-cooled machine and involves ducting the compressor cooling air inlet to the outside of the building. The outside air is then heated by pulling the heat of compression from the compressor fluid and compressed air. For every cubic foot of air pulled in by this heat recovery system, a cubic foot of air that would have to be heated from the outside is eliminated.
Because the plant’s primary heating system does not have to heat the outside air, the savings can stack up considerably. This is a fairly simple, easy-to-install system with typically no need for extensive duct work or booster fans, so the payoff is fast. One note of caution: In cold environments, care must be taken to ensure the outside air temperature is not so low that it will cause the air or moisture in the lines to freeze.
Some heat-recovery systems can automatically recirculate warm air to maintain a constant temperature inside the compressor system. This functionality can also provide a compressor with the ability to operate in unheated spaces as well as maintain a more comfortable exhaust temperature.
Supplementary heat is another use for compressor heat. This heat use supports a plant’s primary heating system. By considering compressor placement and adding ductwork to a compressed-air system, the residual hot air byproduct discharged from an air-cooled compressor can be used to heat the facility in the winter months. In summer months or for operations in warmer climates, the excess heat can be sent outside to help keep the facility cool. In this application, the air is typically heated to a higher temperature than in a pre-heated makeup-air application. More ductwork may be required to distribute the heated air and a higher-flow compressor package fan or added downstream booster fans may be necessary, depending on the size of the facility and the number of compressors contributing heat.
With either application, supplementary or pre-heating, use of a thermostatically controlled heat-recovery system drawing in outside air can increase savings by reducing infiltrations while providing usable heat. A system without this level of control may not be able to heat the outside air enough to provide adequate environment heating.
Depending on the production facility, the heated air may be used for product drying and similar applications. The sky’s the limit as to what function the recovered hot air can provide.
Water-based Applications
While heat recovery from the cooling airflow can be effective, there are other methods to recover and use the heat generated when compressing air. On a water-cooled compressor, the machine is fed water either from a municipal supply or a closed-loop system. This water is used to cool the fluid and compressed-air streams and transfer the heat of compression to the cooling water. This heated water can then be used for various applications such as pre-heated boiler water or process water.
Since a compressor can use significant amounts of water to meet the cooling needs and varying loads can lead to temperature fluctuations, there can be challenges in using the primary cooling water. In this instance, the compressor can be outfitted with an additional heat exchanger to transfer the heat of compression to a supplementary water flow. The flow and temperature of the water can then be more tightly controlled and tailored to the application.
If the compressor’s cooling needs are not being met by this stream of water, its primary cooling system can take up the slack. Additionally, this type of system can be outfitted to an air-cooled machine, allowing heat recovery to a specific water use without the need for a full water-cooled machine. Using water for heat recovery allows year-round use and can recover as much as 85% of the energy required to compress air. This type of system may also offer reduced investment by avoiding the need for extensive ductwork.
Calculating potential savings and payback of a compressor heat-recovery system can vary, depending on the compressor size, operating conditions, local energy rates, use and location of the recovered heat, and the initial investment. For example, a 300-hp compressor can generate 12,378 BTU/min. This represents 7.42 therms/hr. of useable heat, worth as much as $4,000/1,000 hr. of compressor operation at roughly $0.50/therm. Annual heating-cost savings can reach $15,000 without negatively impacting the compressor cooling efficiency.
Whatever your needs for reclaimed heat, the possibilities are many and the energy savings are significant. Using byproducts to maximize efficiency is worth the time and investment.
By Jeremy Sickmiller, Hitachi Global Air Power
Jeremy Sickmiller is Director of New Product Development Engineering at Hitachi Global Air Power, Michigan City, IN (hitachiglobalairpower.com).
The post "Compress Air, Recover Heat" appeared first on Efficient Plant
0 Comments