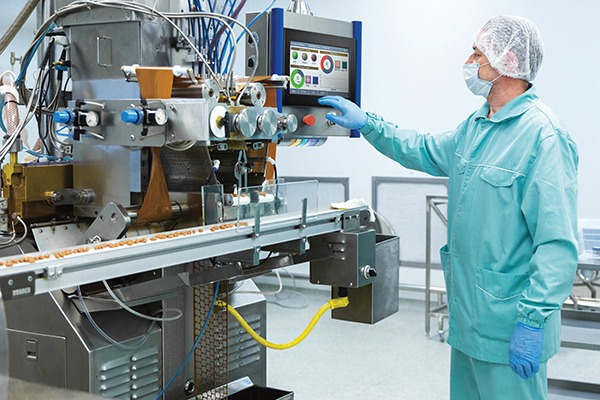
Smart touch-based HMI displays offer advanced technologies for a wide variety of industries, including pharmaceutical, food and beverage, renewable energy, and automotive. Photos courtesy IDEC
Smartphone-like touchscreens and adaptive underlying software provide needed durability and adaptability.
No matter the application, industrial end-users expect intuitive interfaces. For industrial automation, touchscreen HMIs are a mature technology, representing a valuable addition to many machine and process-automation applications. They interact closely with programmable logic controllers (PLCs) and other devices, providing the capabilities of switches, buttons, lights, indicators, and other components commonly found in traditional control panels. Despite this familiarity, every use case for an HMI should be evaluated carefully to ensure products are appropriately selected based on application requirements.
HMI considerations usually begin with display clarity and touchscreen usability. LCD color displays, especially thin film transistor (TFT) types with resolutions of at least 800 x 480 pixels, provide better visibility than their pixelated predecessors. More recently, advanced, flexible, and adaptable HMIs have been introduced that use smartphone-like projective capacitive (PCAP) touchscreens. This technology is superior in many ways to traditional infrared (IR) and resistive touchscreens, which provide only basic functionality.
PCAP touchscreen displays make industrial HMIs much more friendly to the touch. They also allow multitouch gestures that empower operators with information and custom tools, helping them to be more productive while simultaneously increasing safety. PCAP glass requires fewer layers than traditional analog resistive plastic films, facilitating increased light transmission with reduced backlight power for the best degree of visibility and clarity. Some PCAP HMIs provide upward of 500 cd/m2 brightness and a 50,000-hr. backlight life, while also minimizing energy consumption. PCAP glass is also very durable, resists scratches, and will not turn yellow when exposed to UV light. It also has a higher tolerance for cleaning agents.
A PCAP glass touchscreen is durable. The self-capacitance technology prevents accidental input due to particles, water droplets, and airborne debris. Like modern consumer devices, PCAP supports multi-touch input and works even if the user is wearing thin gloves. It has a faster response time than older technologies and is more sensitive and accurate compared with IR.
For many applications, a 7-in. form factor with slim bezel design and flexible mounting options in both landscape and portrait orientation can simplify physical integration and utilization. PCAP touchscreens allow the bezel to be slimmer than is possible with traditional HMIs, providing the greatest amount of display area in the smallest possible footprint and installation depth. This intelligent design a display to be mounted in limited or restrictive spaces such as production lines, medical examination rooms, and automotive dashboards.
From an electrical and physical standpoint, industrial HMIs are most flexible when accepting a voltage range of 12 to 24 VDC, making them suitable for most industrial, solar, and vehicle applications. In the event of a power failure, design features such as MRAM memory can preserve data registers, and a hypercapacitor will maintain clock operation.
Many areas where HMIs are installed, especially in remote locations, experience extreme temperature ranges, so users should look for HMIs rated to operate in a temperature range from -20 to 60 C. To ensure operation in harsh environments such as dirty, wet, or hazardous locations, users must verify an HMI carries the required ratings and approvals, such as IP66/67F, Type 4X, 12/13, UL, CE, and Class I Div 2. When it comes to temperature and environmental ratings, over-specified devices typically provide better performance and longer life in less severe conditions than their light-weight counterparts.
Modern HMIs, equipped with connectivity and communications, including a built-in web server, are effective for IIoT applications and provide additional visualization options through browser interfaces and mobile devices.
Connectivity
Comprehensive connectivity options are needed so an HMI can be adapted for any industrial application without extensive modifications to systems and platforms. For maximum flexibility, modern HMIs should be outfitted with at least two USB Type-A ports, serial connectivity (RS485/422 and RS232C), and an Ethernet port. While many traditional HMIs use screw-terminal connections for power and communications, push-in wiring connectors provide a more contemporary approach for easier installation and service, and better reliability in high vibration environments.
An operating system that can take advantage of USB ports for advanced Linux-compatible accessories—such as Wi-Fi and Bluetooth dongles, speakers, sensors, cameras, and barcode readers—provides additional application options. For example, a USB speaker can be added to provide speech output notifications to receive status updates, which improves efficiency.
Communications and IIoT
Beyond physical connectivity, an HMI must support the right communication protocols. There are many such protocols, some relatively “open” and others very specific to certain makes and models of target devices. The most adaptable HMIs support more than 100 serial and Ethernet industrial communication protocols, including popular variants like BACnet IP, EtherNet/IP, Modbus RTU Master/Slave, and Modbus TCP/IP Client and Server.
Additionally, HMIs should support multiple protocols simultaneously so users can exchange data with several clients and servers in real time. This makes them ready for industrial internet of things (IIoT) applications.
No modern discussion of HMI connectivity is complete without addressing the various ways users can remotely access displays. A built-in web server is a common means for providing access to remote users through PCs, tablets, smartphones, and any other device with a web browser. Custom HMI web pages require no special software, and this form of interface can differ from what is displayed locally on the HMI itself, providing more options for users to visualize the right information wherever they are located. Remote connectivity helps improve operations, troubleshooting, and maintenance efforts by including team members who are not locally located at a machine.
Expansive connectivity provides more design options. For instance, a USB-connected speaker can provide speech output notifications, so workers can receive touchless status updates.
Intuitive software
In many regards, hardware is only as good as the software, but it is critical that both elements work well together to maintain efficient operation. Ease of configuration is another aspect to consider, as simple configuration procedures reduce training requirements.
For this reason, designers should investigate the look and feel of an HMI development environment in addition to the resulting graphics. The best configuration software is easy to use, with minimal training, and is applicable to many makes and models of HMI. This empowers engineers, managers, and plant operators to implement and execute new applications on a variety of HMI hardware types using a single software package. Drag-and-drop options add to configuration simplicity with built-in symbol libraries that enable the creation of cutting-edge graphics with easy-to-navigate tabs and drop-down tables.
HMIs need not be complicated, application-centric, or expensive to integrate and maintain through multiple product lifecycles. End users desire a visualization and touchscreen experience that is clear and familiar, and developers look for HMIs that are straightforward and practical in design, while packing in the latest technologies in an easy-to-use manner. This means incorporating robust OT-capable HMIs that mimic the IT feel of smartphones, with industry platform integration that works seamlessly using the preexisting connectivity infrastructure found in every up-to-date facility. EP
By Linda Htay, IDEC Corp.
Linda Htay is Automation Product Manager, IDEC Corp., Sunnyvale, CA (us.idec.com). She has more than 15 years of experience working with automation and industrial products such as HMIs, PLCs, touchscreens, and display products. Htay holds a BS degree in Electrical Engineering.
The post Advanced Touchscreens Enhance HMI Versatility appeared first on Efficient Plant.
The post "Advanced Touchscreens Enhance HMI Versatility" appeared first on Efficient Plant
0 Comments